Director of Quality Assurance
Director of Quality Assurance
The Director of Quality Assurance is responsible for ensuring that WFM’s Quality Management System is established, implemented, and maintained in accordance with ISO 9001;2015. They must understand and implement all WFM's customer quality requirements.
Roles & Responsibilities:
- Acts as a management representative of the QMS
- Creates, approves and controls internal and external quality documented information
- Responsible for reviewing requirements with estimating to ensure we have the ability to meet product and service requirements during the Contract Review process. Also reviews all contracts prior to release in the shops
- Determines traceability requirements to ensure conformity of products and services
- Responsible for controlling and recording customer property. Also contacts customer in the rare event customer property becomes lost, damaged or unusable.
- Essential role in bi-annual Management Reviews
- Responsible for the coordination, recording and monitoring product quality, non-conforming material, measuring and testing equipment, document control and distribution, planning and developing production processes, special processes, inspection processes, approving suppliers and vendors,
- Responsible for establishing and monitoring, and recording training for employees and quality control personnel.
- Responsible for having systems in place to control production provisions to include product requirement information, work instructions, suitable production equipment, monitoring and measuring equipment, validation processes, identification, and traceability to final shipping requirements.
- Responsible for ensuring non-conformances are tracked and corrective and preventative actions are established, recorded and implemented.
- Responsible for planning and conducting internal quality audits to verify the implementation of established program requirements and to determine the effectiveness of the QMS
- Manage all NDT/NDE and machining quality control inspectors and personnel.
- Schedule and host customer quality control inspections/visits/hold points.
- Review the need for development of new or revised Quality Manuals and project manage any new quality certifications WFM chooses to obtain (NAVSEA, AISC, etc).
- Continual development of processes and procedures to improve product quality and on-time delivery.
- Develop and maintain a strong relationship between Quality and Production
Abilities/Qualifications:
- Ability to provide clear leadership and motivate the team
- Ability to think strategically
- Ability to communicate clearly
- Ability to guide and direct others
- At least 5 years’ experience in an ISO 9001 manufacturing environment working in Quality Control
- Must be highly organized with excellent listening and problem-solving skills
- Strong ethical background
- Must be very observant and pays keen attention to detail
- Ability to conduct data analysis and reporting
- Must keep excellent records
Company Benefits:
- Healthcare/Dental/Vision Full Family Coverage with multiple plans for you to choose from
- Insurance Opt-out Payout
- Employer-paid Life Insurance
- 401k Company Match up to 4%
- Vacation in the first year of service
- Monthly Attendance Bonus
- Bi-Annual Company Bonuses
- Double Time Pay for Sundays and Holidays
- Company Paid Training and Certifications
- 10% Shift Differential
Job Types:
- Full-time
- Part-time
Schedule:
- 10-hour shift
- Overtime
- Weekend availability
Supplemental pay types:
- Bonus pay
- Signing Bonus
Ability to commute/relocate:
- Hubbard, OH 44425: Reliably commute or planning to relocate before starting work (Preferred)
Experience:
ISO 9001: 5 years (Preferred)
Work authorization (Preferred)
Shift availability:
- Day Shift (Preferred)
- Night Shift (Preferred)
Work Location:
- One location
Join Our Team
Apply Now
(800) 827-0596
careers@warfab.com
Warren Fabricating has been a major part of my life. I’m going on 10 years now, I’ve gotten married, and I now have two children whom I love very much. It’s always been a balance of work and life, and I think it’s a good balance. I really enjoy what I do here day to day so it makes it easier to go home when you’re not stressed when you leave work for the day.
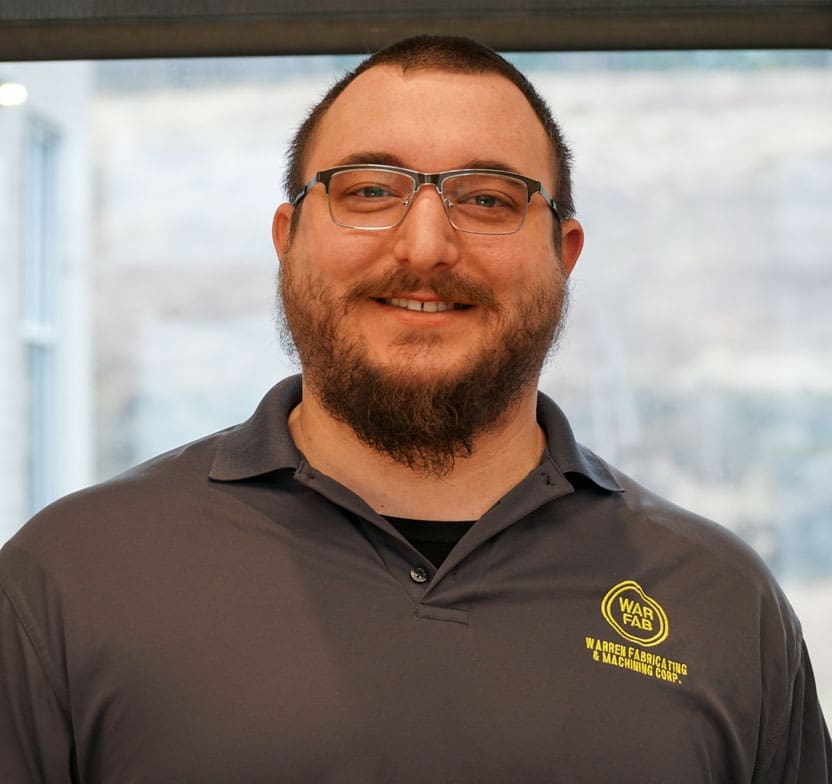
Jordan Cline
Project Manager
I think having a strong team is what makes us so amazing. The dedication and the loyalty of our employees is what makes us who we are. They are there for us and we are there for them. It’s always been important to us as owners to provide good quality healthcare, life insurance benefits, guaranteed overtime; all of the things that people need. You really need to take care of your people in order to be successful today.
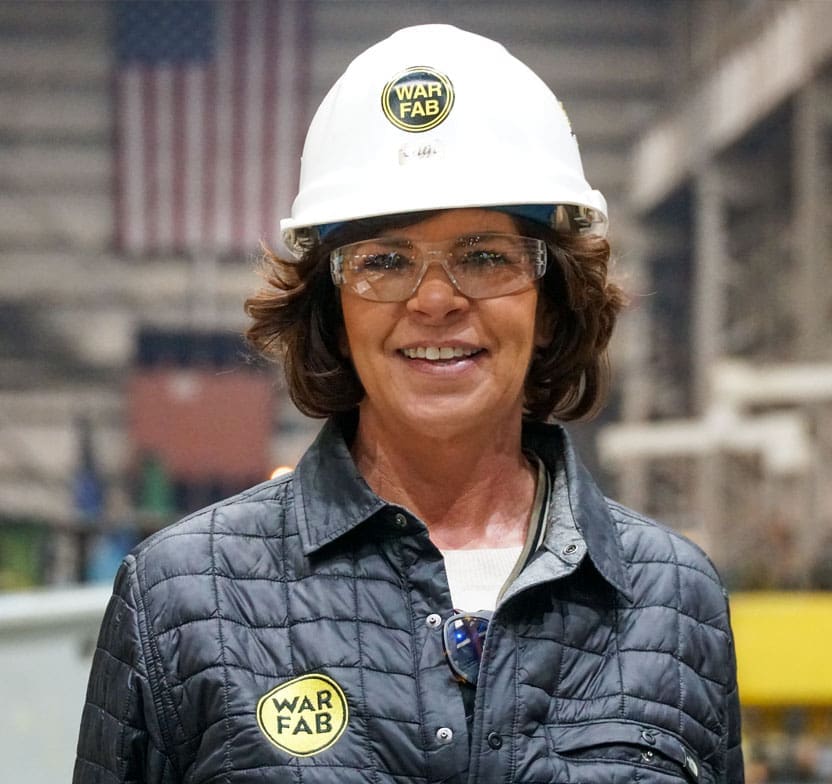
Regina Rebhan
Owner